
QUALITY
Ramco Fitting Industries is devoted to meeting or exceeding customer expectations by continuously improving its Quality, Delivery, and Cost in Stainless Steel with the help of senior management and all staff. Our primary goal is to create and manufacture the most dependable industrial goods to assist our clients in developing the most efficient applications. All of our goods are subjected to various quality checks and testing.
We are committed to meeting our customers' requirements and demands with high-quality items at the most affordable pricing. Everyone in the firm is accountable for delivering high-quality products and services and has the resources to do so. We strongly and solely believe in the principle of quality management for industries that help us in improving and maintaining the products and services quality.
The Ramco Fitting Industries staff is always working to improve and maintain the effectiveness of our Quality Management System. To achieve our quality goals, each employee, as well as the company's owner, is committed to:
-
Listen to and respect our client's demands and wants.
-
When it comes to quality, do not accept compromise.
-
To assure 0% client complaints
-
design and create each product in accordance with the client's expectations.
-
Ascertain that our client's complete pleasure has been attained.
TESTING FACILITY
Ramco Fitting Industries is renowned in the manufacturing sector for its exceptional precision fittings and comprehensive testing facilities. With a commitment to quality and reliability, we leverage advanced technologies to ensure that every product meets stringent industry standards. Our extensive range of testing capabilities includes PMI (Positive Material Identification) testing, ultrasonic testing, D meter testing, and more. These testing methods play a crucial role in assuring the integrity, durability, and safety of our fittings, catering to diverse industrial needs across various sectors.
Positive Material Identification (PMI) Testing:
PMI testing is a vital process in the manufacturing of fittings at Ramco Fitting Industries. This non-destructive testing method verifies the chemical composition of materials used in our products. By employing handheld X-ray fluorescence (XRF) analyzers and other state-of-the-art equipment, we ensure that the materials conform to specified standards and requirements. PMI testing not only enhances the quality assurance process but also contributes to the traceability and reliability of our fittings in critical applications.
​Ultrasonic Testing: Ultrasonic testing is another essential facet of our quality control procedures at Ramco Fitting Industries. This non-invasive technique utilizes high-frequency sound waves to detect internal defects such as cracks, voids, and inclusions within our fittings. By employing advanced ultrasonic testing equipment and skilled technicians, we can accurately assess the structural integrity of components without causing damage. This method is particularly crucial for ensuring the safety and performance of fittings used in demanding environments such as oil and gas, aerospace, and automotive industries.
​
D Meter Testing: D meter testing, also known as thickness testing, is employed to measure the thickness of materials used in our fittings. This ensures that components meet specified dimensional requirements and can withstand operational stresses and pressures. At Ramco Fitting Industries, we utilize precision D meter instruments to conduct accurate measurements across various types of materials, including metals and alloys. This testing process is integral to maintaining uniformity and reliability in our product offerings, thereby enhancing customer satisfaction and trust.


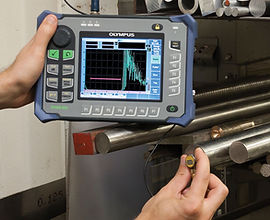

